Foster pioneers 3D concrete printing with contractor
Written by: Laura Mark
Publish Date: November 25, 2014
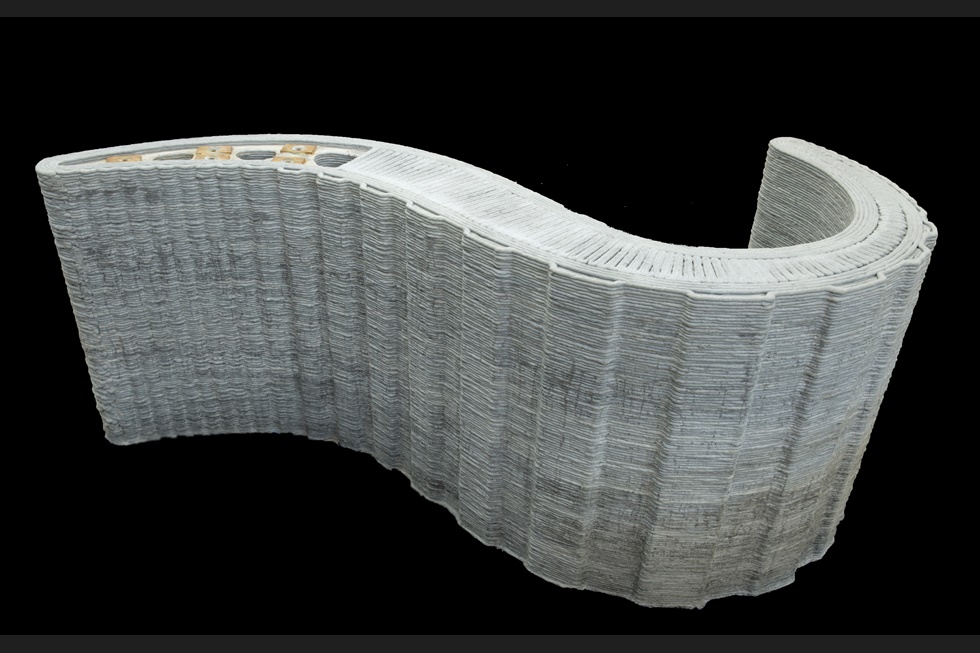
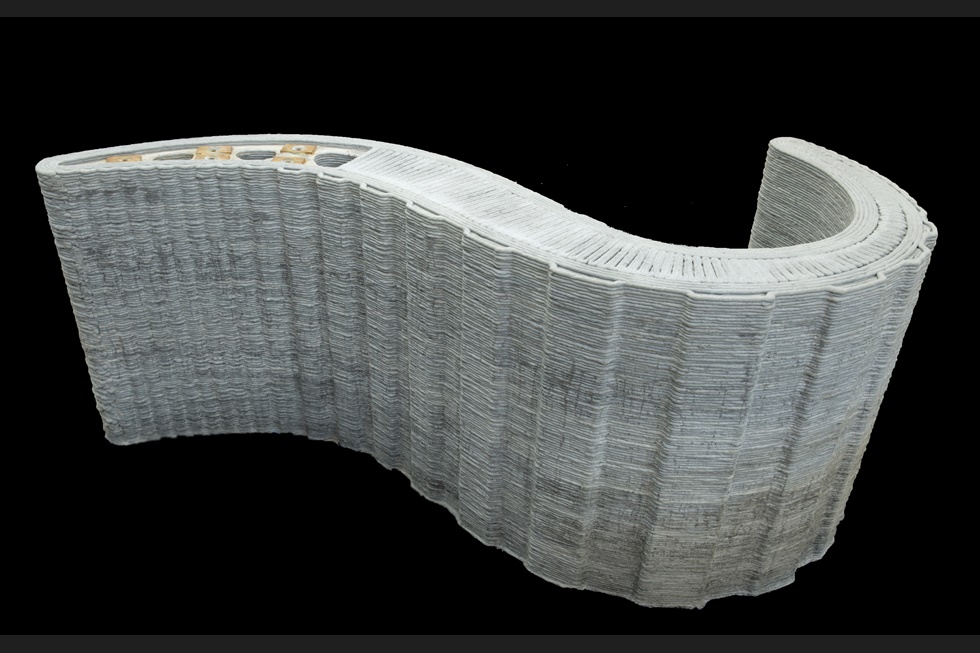
The contractor has signed an agreement with Loughborough University, which has been working on the development of 3D printing for the construction industry since 2007.
The agreement will allow Skanska to use 3D concrete printing technology in real construction applications.
The technology, which has been developed by a team of collaborators including Foster + Partners, Buchan Concrete and Lafarge Tarmac, deposits a high–performance concrete precisely under computer control.
The 3D printers are fitted to a gantry and a robotic arm and deposit layers of concrete to create complicated components.
According to Skanska, the printer can make things which cannot be manufactured by conventional processes such as complex structural components, curved cladding panels and architectural features.
The team will now spend 18 months developing a commercial concrete printing robot alongside a 3D printing supply chain.
Rob Francis, Skanska’s director of innovation and business improvement said: ‘3D concrete printing, when combined with a type of mobile prefabrication centre, has the potential to reduce the time needed to create complex elements of buildings from weeks to hours. We expect to achieve a level of quality and efficiency which has never been seen before in construction.’
Richard Buswell from the Building Energy Research Group at Loughborough University added: ‘We have reached a point where new developments in construction manufacturing are required to meet the new challenges and our research has sought to respond to that challenge.
‘We have been convinced of its viability in the lab, but it now needs the industry to adapt the technology to service real applications in construction and architecture.’
FOSTER PIONEERS 3D CONCRETE PRINTING WITH CONTRACTOR
About the Author
This article is written by Laura Mark
Read the original post here.